在制造业的日常运营中,经常会碰到这样的问题:需求发生变化时,哪些物料可能面临短缺的风险?一旦缺料成为现实,如何调整生产,才能利用现有资源获得最大的收益?如果物料到货能够提前一周,可以保证多少订单及时交付?
要回答这些问题并不容易,特别是在涉及数百种物料的复杂制造环境中,传统的管理方法和软件系统往往难以应对。然而,随着智能决策工具的出现,这些问题的解决变得可能。本文将通过分享最佳实践案例,展示如何利用这些工具进行供需模拟和场景分析,以迅速响应市场和需求的变化。
该案例企业是一家国内的扫地机器人公司。其产品生产过程复杂,涉及众多组件。采购部门需要提前协调多个供应商,确保原料供应及时且充足。由于生产BOM复杂、原材料众多且产品共用组件多,人工难以快速判断哪些原料存在缺口,也难以决定需要采购或协调交货的时间。因此,需要决策工具来辅助计算供应现状,定位供应瓶颈,并明确不同采购参数限定下的供需结果。下面通过一个简单案例具体说明。
假设我们需要生产四种成品:P01、P02、P03和P04,生产物料清单(BOM)说明和示意图如下:
- BOM包含两个层级,涉及多种原料(M01-M08)和两种半成品(B01-B02)。
- 原料M02在两个半成品、原料M05在所有成品的生产中均有使用。
- 半成品B02用于三种成品的制造。
- 其他原料和半成品仅用于一种成品或半成品的生产。

当前业务人员需要根据成品需求制定三个周期(一个周期为一个自然周)的生产计划。需求计划及其他重要输入数据如下表所示。其中需要注意的是半成品B01在第一个周期有1000件外部流量,即在途库存。所有物料中,只有原材料允许采购,半成品与成品均需要通过生产获得。其中原材料M05和M06的采购时长大于等于一个周期,即Lead Time ≥ 1, 也就是当周期采购的量至少下一个周期才能入库使用。表格中的产品价格对于原材料为采购价格,对于成品为成品价值。
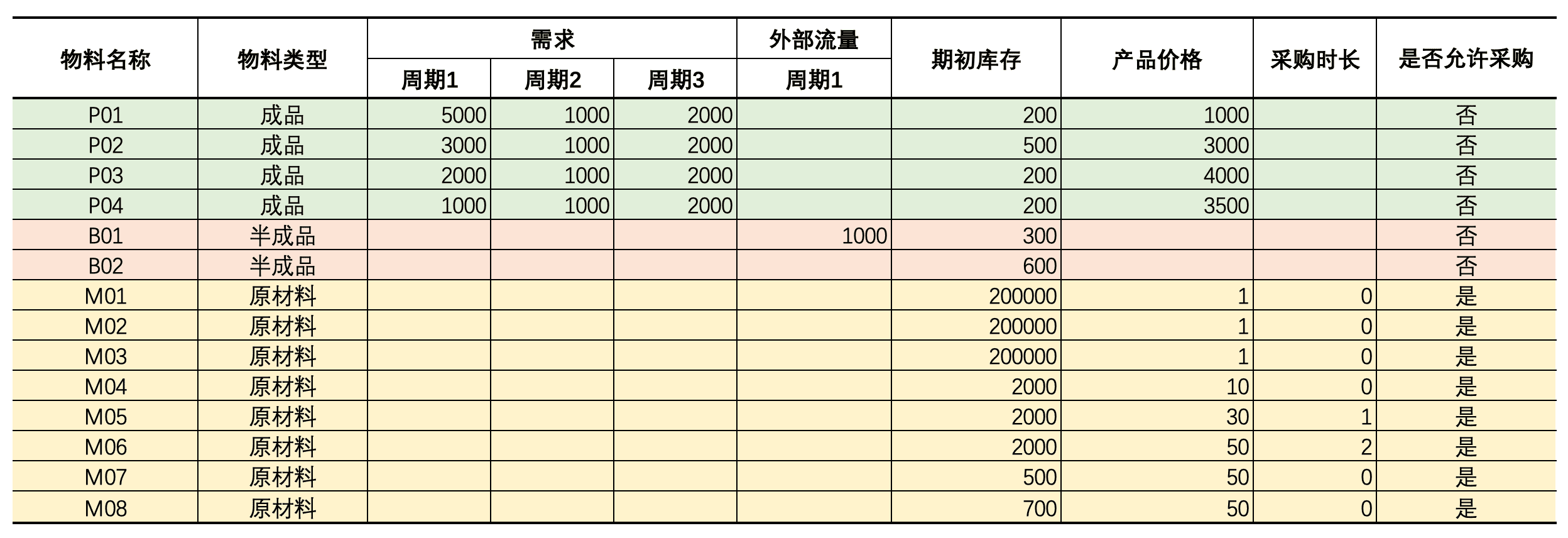
回顾刚才的问题:基于当前的物料库存、采购策略、产能情况,可以支持的需求供应的上限是多少?与需求计划之间有多少缺口?瓶颈在哪里?这些问题是否让你感觉可以计算,但可行解又太多而无从下手?让我们借助小流智算平台的产销协同与供应链主计划应用来解决这些问题。
当我们把当前的采购策略、库存水位、BOM约束、产线产能和需求计划等数据输入到优化工具后,可以选择不同的需求满足目标。系统默认的求解目标是最大化需求满足的数量,即最小化需求缺口。如果当前供给不能满足全部需求,则在最大化需求满足数量的基础上,对同等优先级的不同产品需求采用公平分配策略(fairshare)。
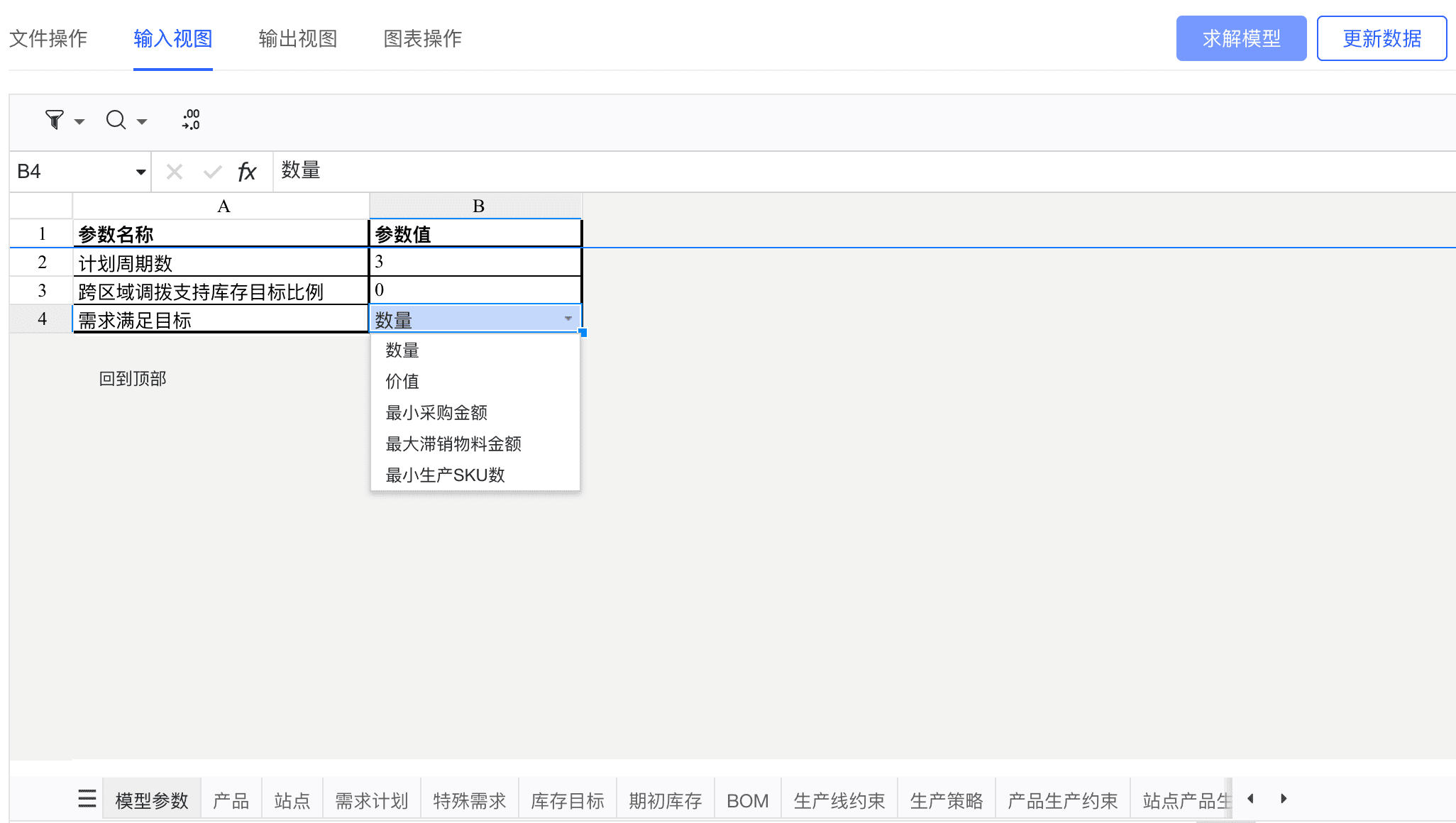
例如,对于案例中的给定数据,如果我们选择最大化需求满足数量的求解目标,则会得到下表中的结果。当前的供给无法满足所有需求,所以模型会平衡不同产品之间的生产量,保证每个产品最终满足需求的比例相同,即每个产品期初库存加生产量再除以需求计划的比例相同。

如果选择其他的求解目标,模型会做出不一样的分配结果。例如,如果我们的目标是最大化需求价值的满足,则模型会保证最终满足需求的成品的总价值最大。从下图中的输入中可知,对于四种成品的价值排序由高到低为P03、P04、P02、P01。在这种目标设定下,结果表显示,尽管四种成品的总生产量与之前的场景相同,均为2000件。但生产决策会有所调整。模型会首先确保价值最高的成品P03的需求得到满足,然后再依次考虑价值较低的成品。这种策略将持续进行,直到所有物料库存或产能被充分利用,或者所有成品的需求得到满足。
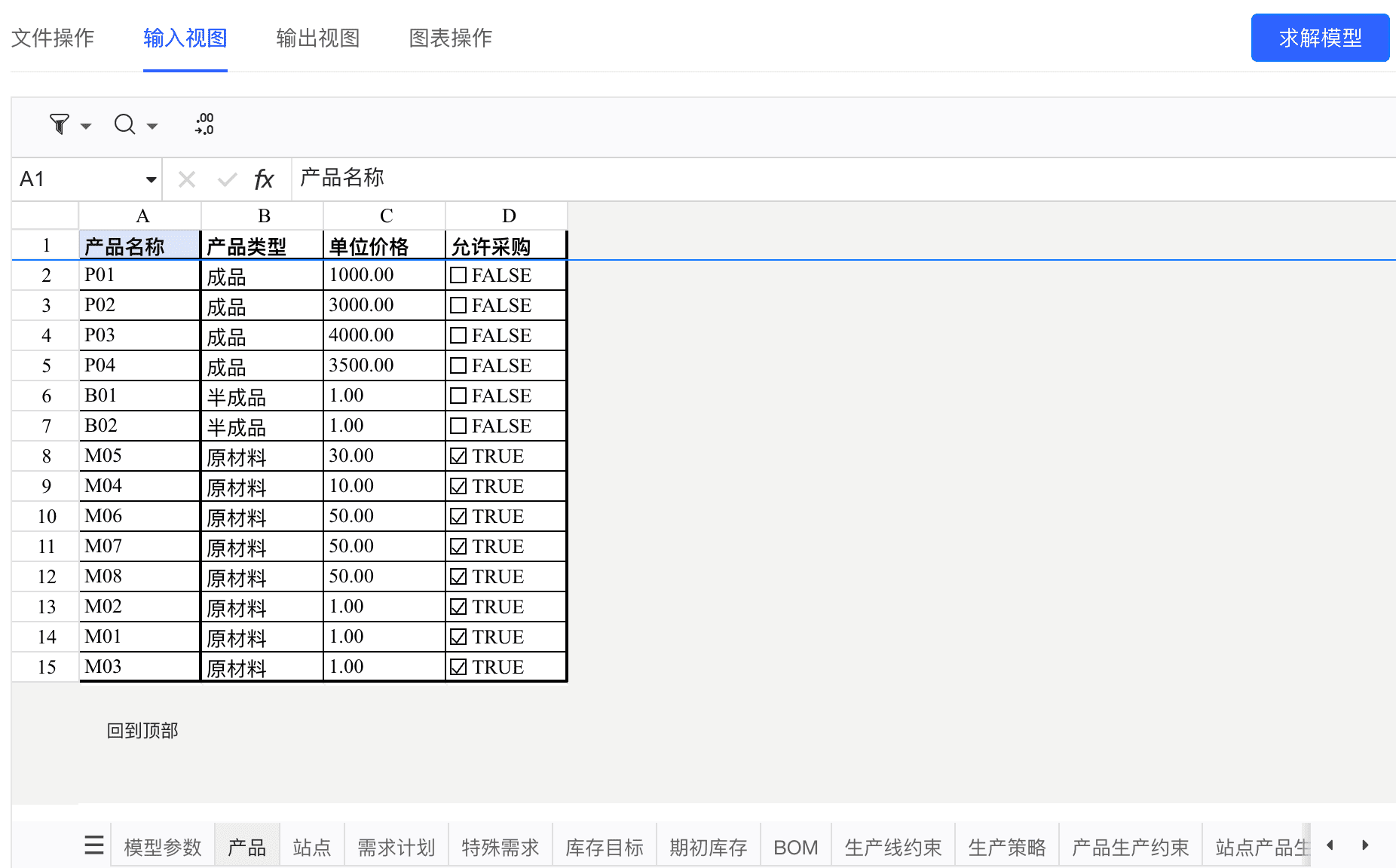

如果选择最大化呆滞物料消耗的求解目标,另外还需要在物料消耗策略中定义呆滞物料列表。如下图所示,如果我们定义原材料M04为呆滞物料(其期初库存为2000),则在求解中,模型会优先考虑能消耗该原料的生产。如结果所示,同样总成品生产量为2000,在最大化呆滞物料消耗的求解目标选择下,模型选择生产的产品为P01,即能消耗呆滞原料M04的生产决策。
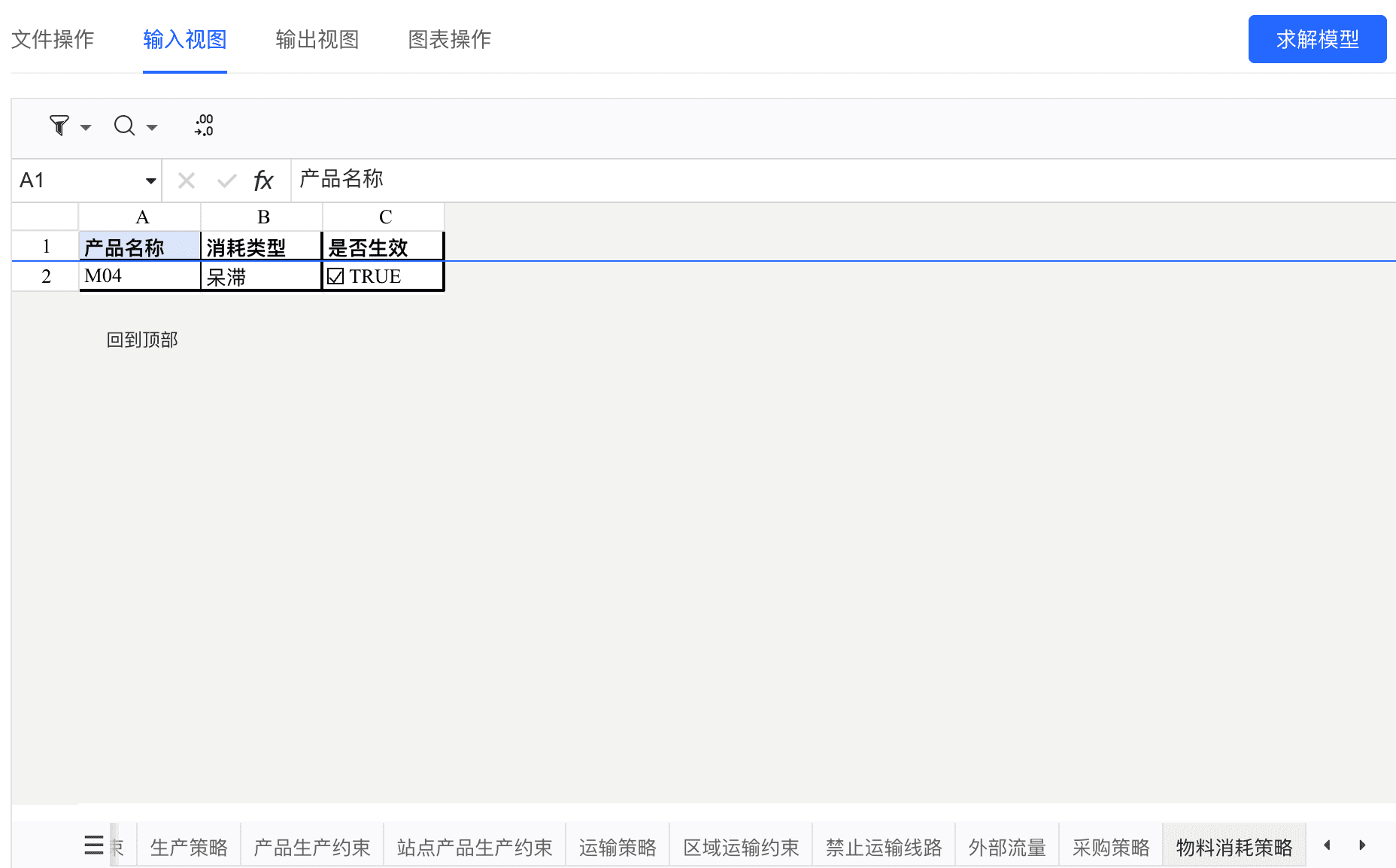

除了以上提到的求解目标,产销协同与供应链主计划应用还提供最小化采购金额、以及最小化生产SKU数量的求解目标。需要注意的是,这两个求解目标以及最大化呆滞物料消耗的目标都是在最大化满足需求数量的基础之上,在不同产品间做进一步资源分配时所要满足的目标,最大化需求满足依然是模型求解的第一优先原则。
从以上结果我们可知,当前供应不足以满足所有成品需求。这种供不应求的现状,可能是由产能不足造成,也有可能是因为物料供应不足造成。从下图的产能输出中可以看到,当前使用的产能不到总产能的1%,所以可判断供不应求的现状是由于物料供应不足造成的。
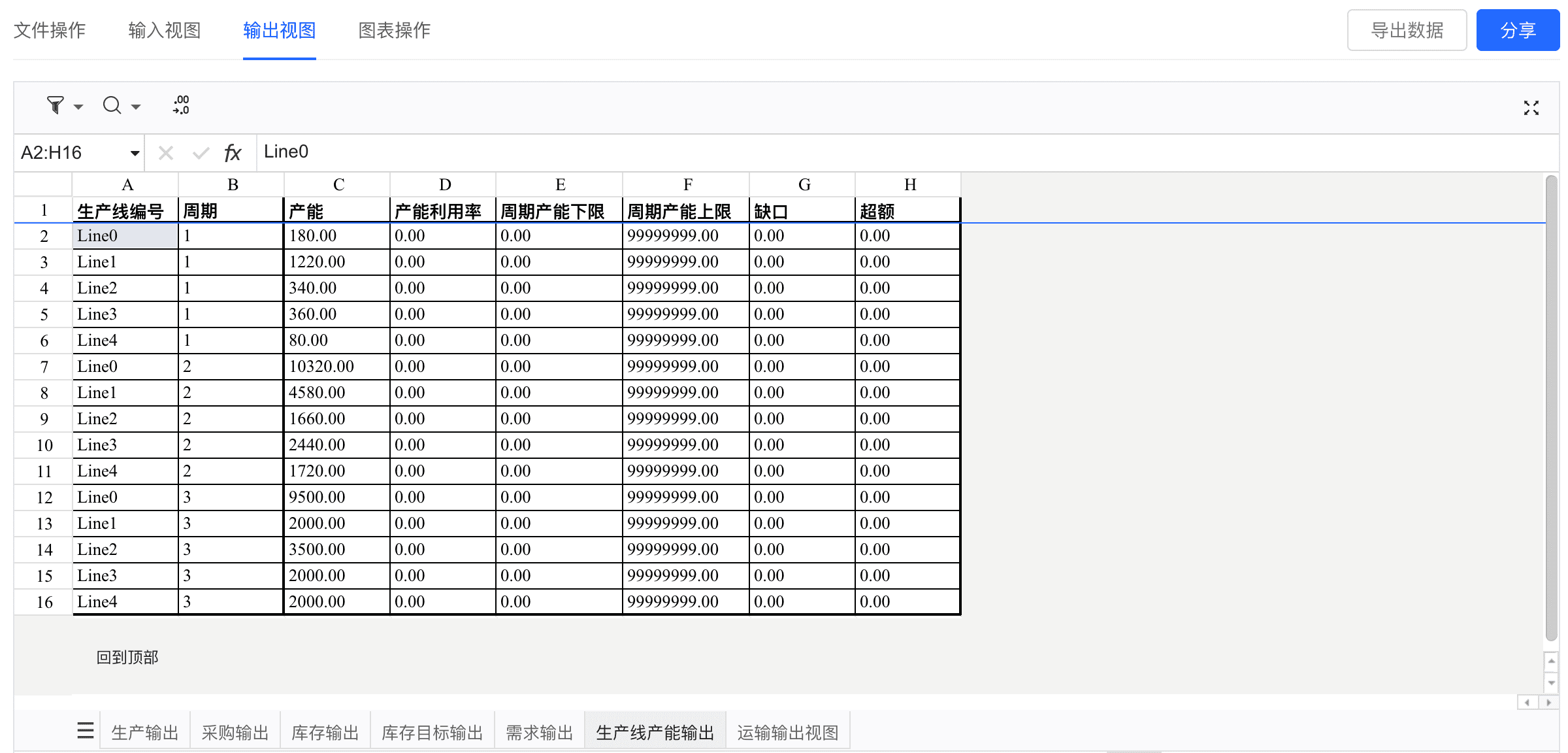
由于产能足够,交货时长在1个周期之内的物料都可以被视为库存充足。限制生产的物料只有可能是交货周期大于等于1的M05和M06(M05采购Lead Time为1,M06采购Lead Time为2),但这两种物料的缺口数量我们无法直接从上一步的结果中获得。如果想知道这两个物料距离满足所有需求的缺口是多少,可以通过修改输入参数配置来实现。
将采购策略中这两个物料的输入设置为不生效,则系统会采用默认的交货时长0,即默认所有可采购的物料当周都可以交货。缺少的物料则会通过当周期采购的方式进行补货,通过查看采购结果,我们就可以得到为了满足所有成品需求,需要补充的物料缺口是多少。
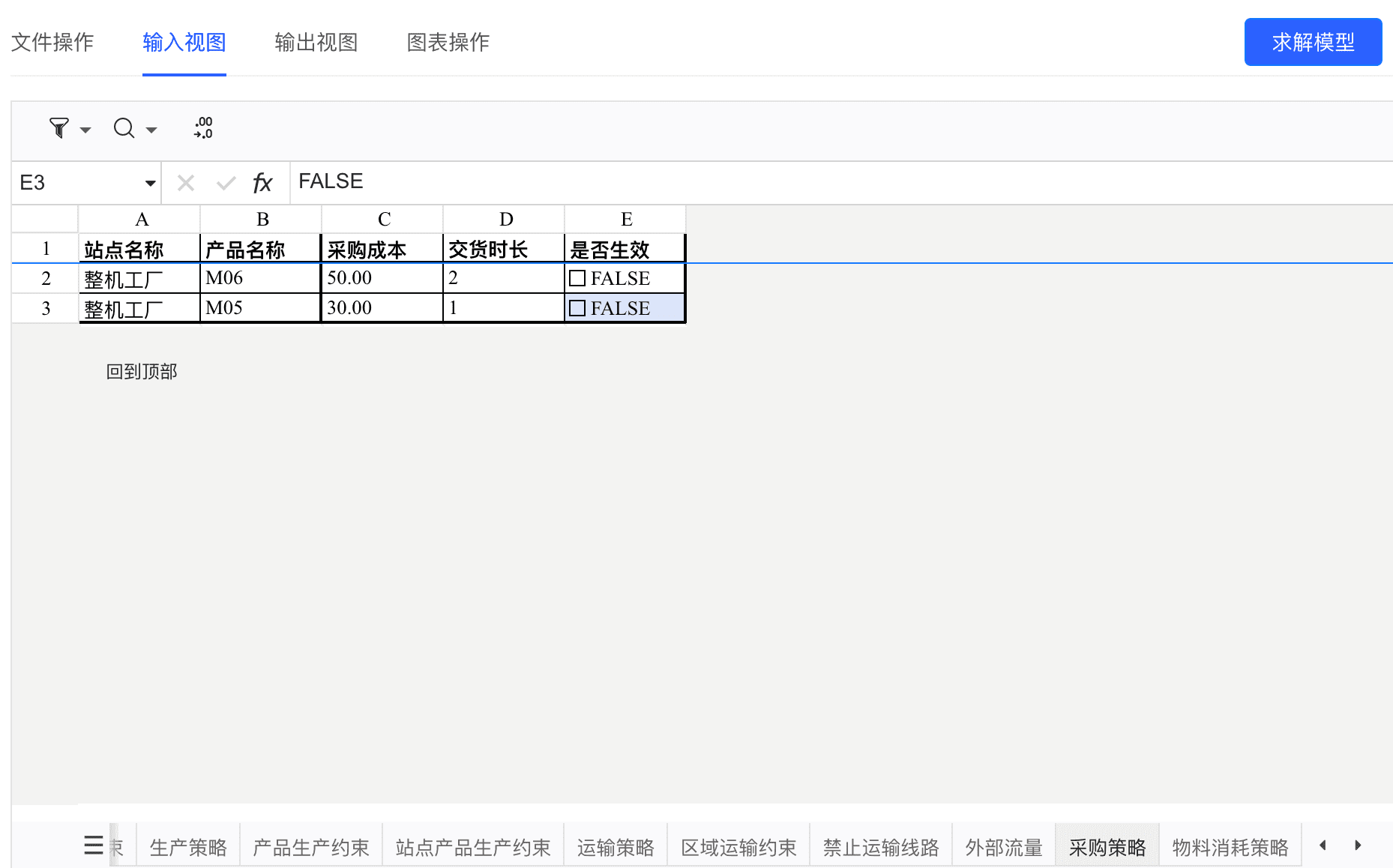
如下图所示,为了满足第一个周期的所有需求,M05的物料缺口为7900,M06的缺口为500。如果可以得到及时的供货补充,新生产的产品加上成品期初库存则可以满足所有需求。
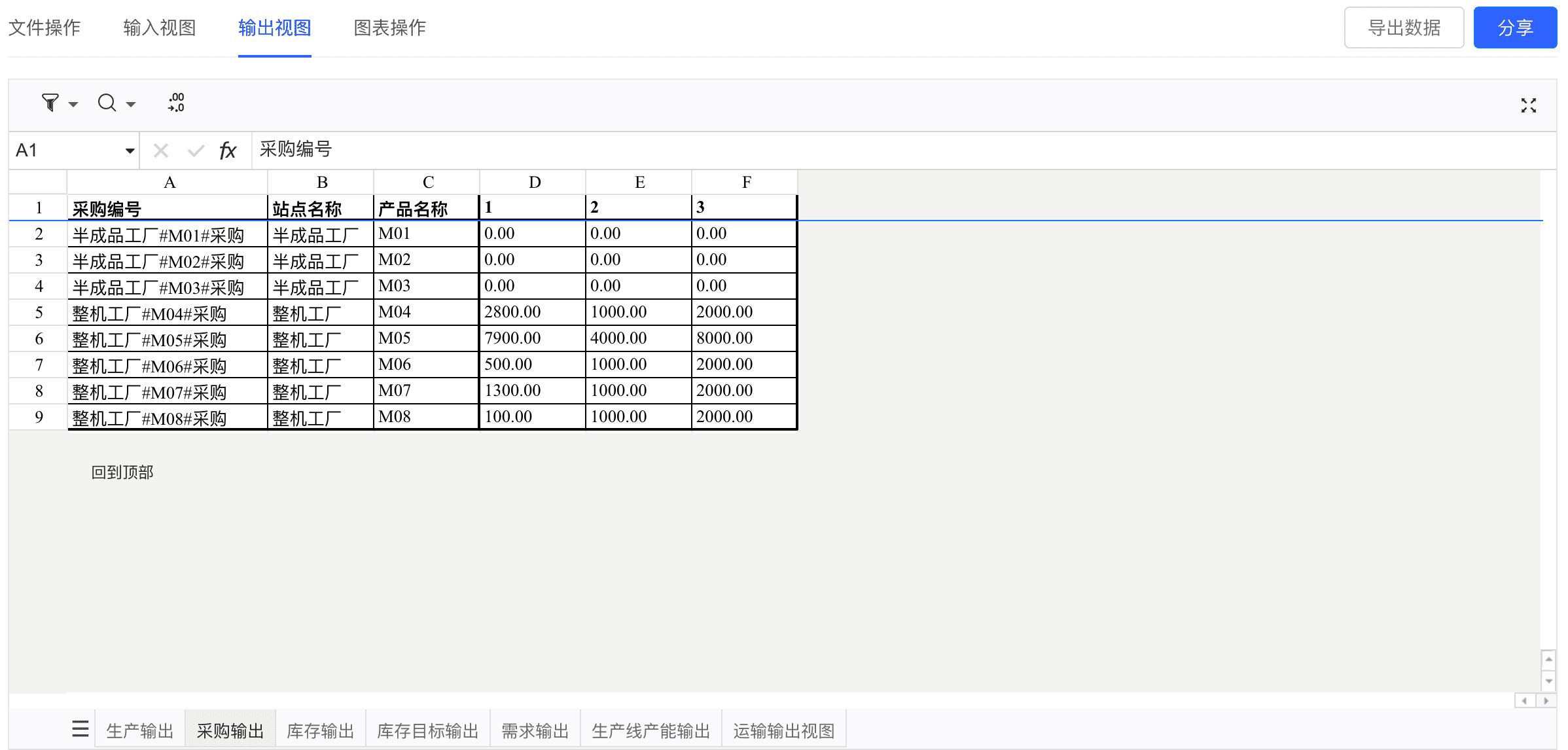
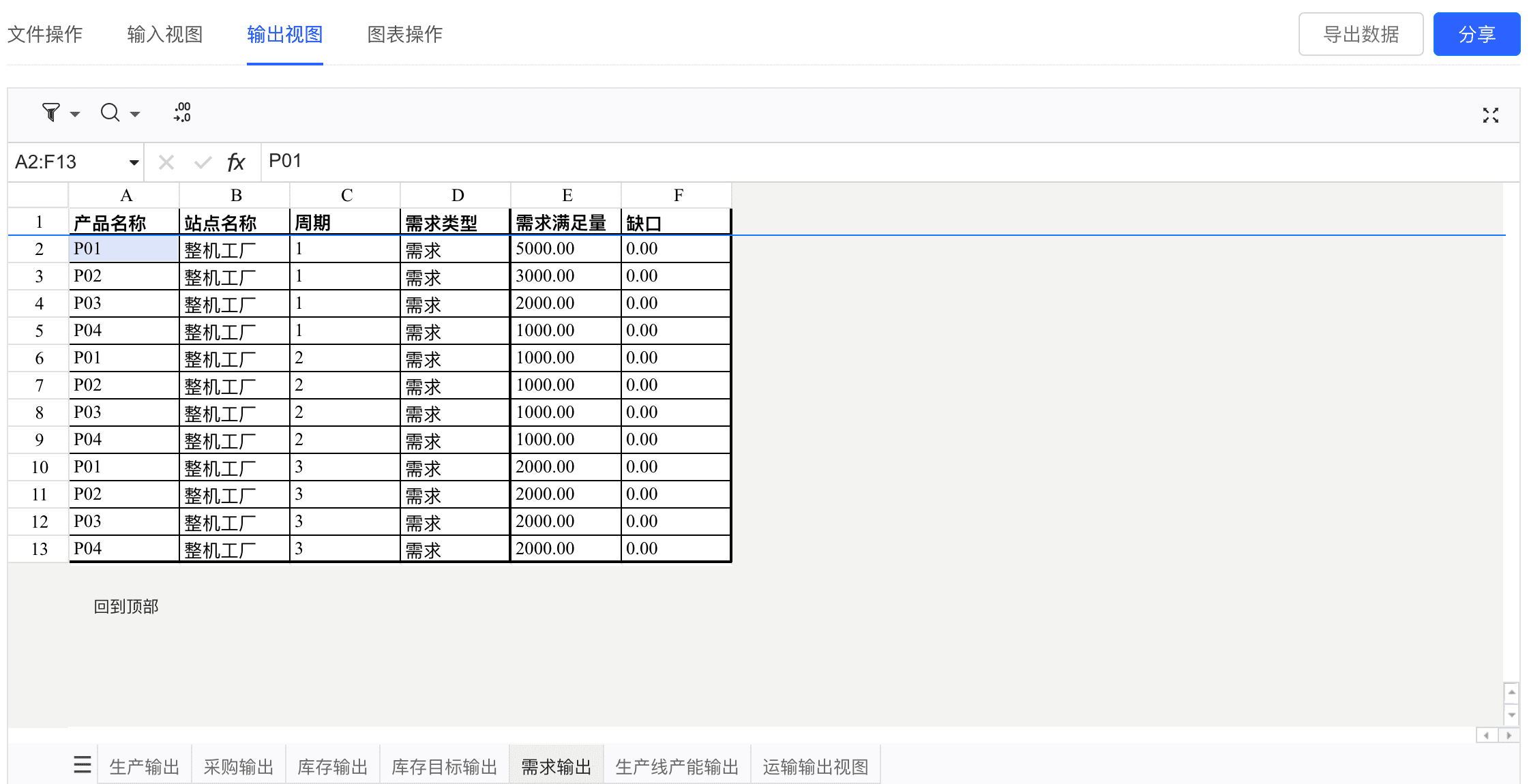
让我们进一步探讨这个案例:当前的需求缺口在于原材料M05和M06的采购,如果能够与供应商达成及时供货的协议,我们将能够满足所有的末端需求。然而,现实中由于供应商产能和物流限制等原因,可能无法立即供应所有所需的物料,也许通过协商,有可能确保部分原料的供应。例如,当前M05在第一个周期的缺口为7900,通过协商,供应商可以在第一个周期加急供应3000的货量,剩余部分依旧需要等待一个周期之后到货。
针对这种情况,可以在应用输入中增加3000个M05的外部流量,模拟第一个周期可以加急供货的场景,并进行求解得到新的供需满足情况。
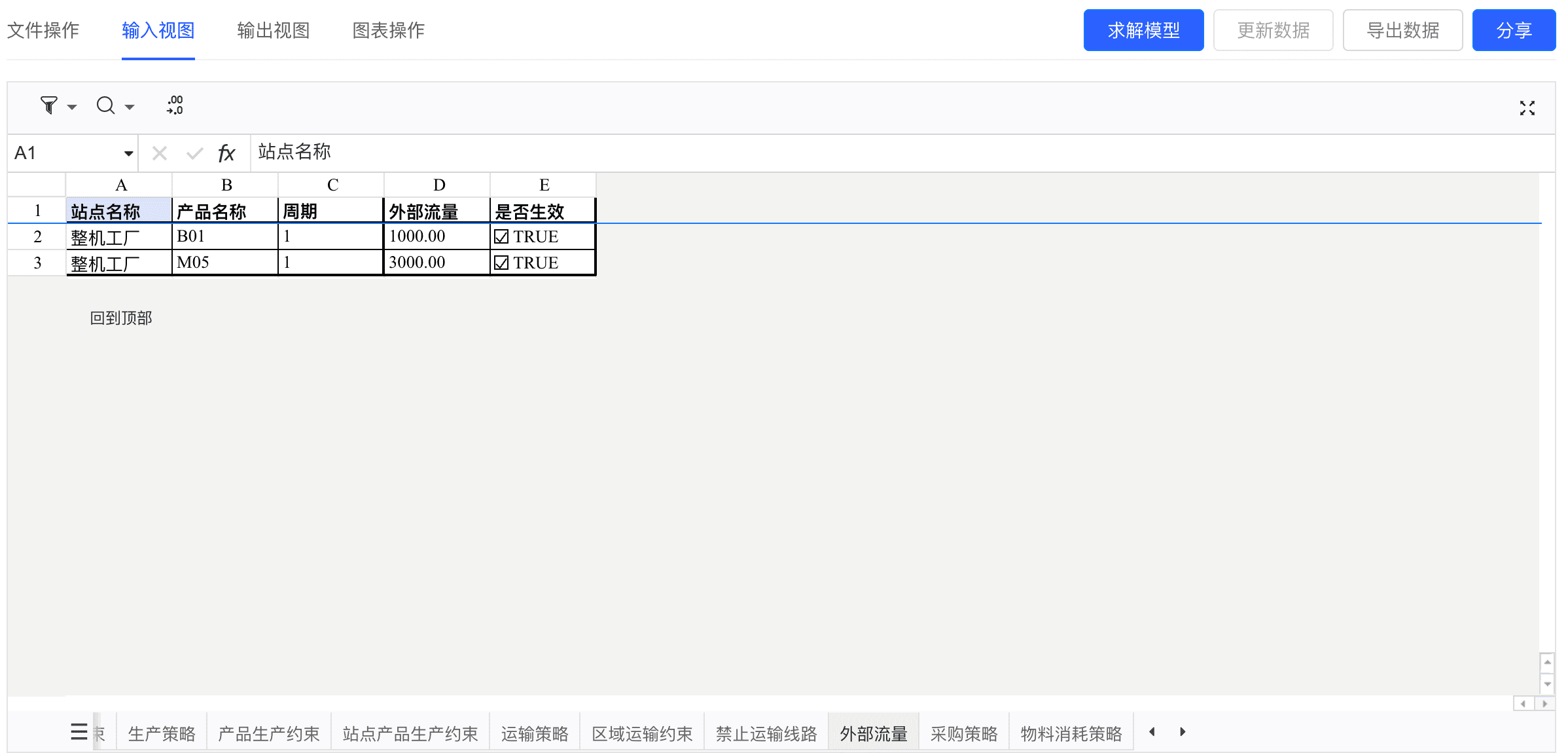
设置求解目标为最大化需求满足数量,从以下表格中的结果可以看到,由于3000个M05的加急供应,第一个周期的需求满足比例已经由原来的28%上升到55%。同时也可以根据模型输出的采购结果对所有原材料进行采购计划的沟通和制定,以满足当前周期以及未来2个周期的生产。

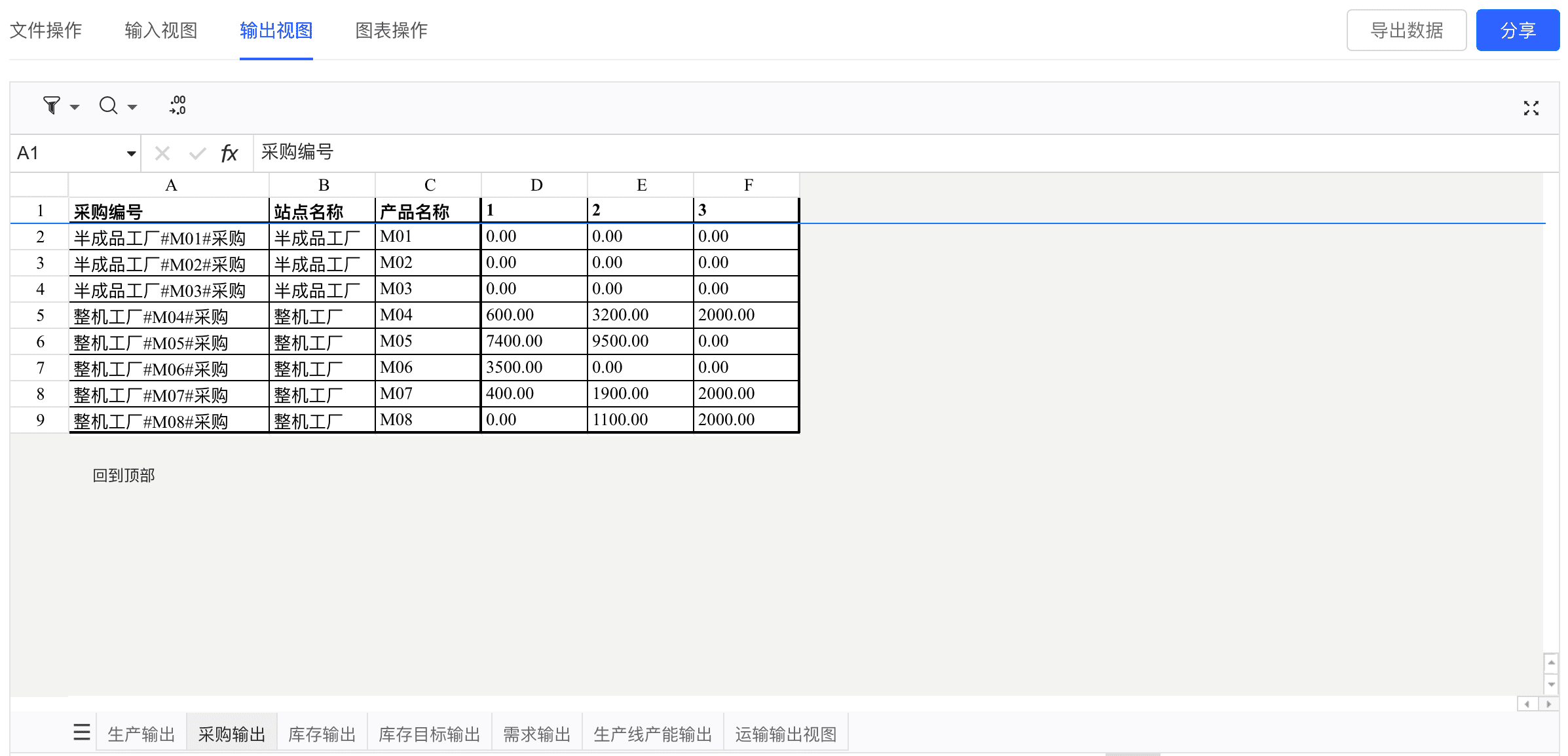
采购计划的制定往往是经过多轮协商和沟通的结果。在这个过程中,产销协同与供应链主计划的应用可以发挥重要作用。它们作为辅助工具,能够提供不同场景下的供需模拟结果,为决策者提供更精确的数据支持。
通过以上案例,我们演示了怎样利用智能决策工具来模拟供需状况、定位供应瓶颈,并对不同的解决方案进行评估,作为辅助工具协调各部门最终达成供需平衡。在实际应用中,可能面临更复杂的场景,包括更多的产品和物料、更复杂的物料清单(BOM)系统,以及工厂产能和下游物流网络的限制。然而,解决问题的整体思路和步骤基本保持一致。
需要注意的是,这个过程不是一次性的。业务人员必须根据运营策略和市场需求的变化,持续进行优化和调整,这样才能确保供应链的灵活性和效率,从而在动态的市场环境中保持竞争力。
如果有相关需求,欢迎试用小流智算“产销协同与主计划”应用。PC端可登陆网址 https://convect.cn/ 注册账号免费试用,移动端可扫描以下二维码添加客服微信号详询。